Geehy has introduced the APM32F035 motor controller solution for electric two-wheelers, emphasizing key factors such as range, intelligence, humanization, and cost performance. This mass-produced solution incorporates features like Hall capture, self-learning, braking, reversing, cruising, gear speed regulation, and anti-theft alarm. Extensively tested for hardware design, including control, sampling, drive, and communication circuits, as well as the system-level development ecosystem, it effectively meets the design requirements of electric two-wheelers.
Based on the APM32F035 motor-dedicated MCU, Geehy’s solution supports a sensor-based FOC strategy and integrates multiple op-amps and comparators. This simplifies peripheral circuit design, reduces interference, and achieves high efficiency with low noise. The APM32F035, as the main control chip, samples bus voltage, current, and HALL signals, executes motor control logic, and communicates with the upper-layer application, providing operational status feedback.
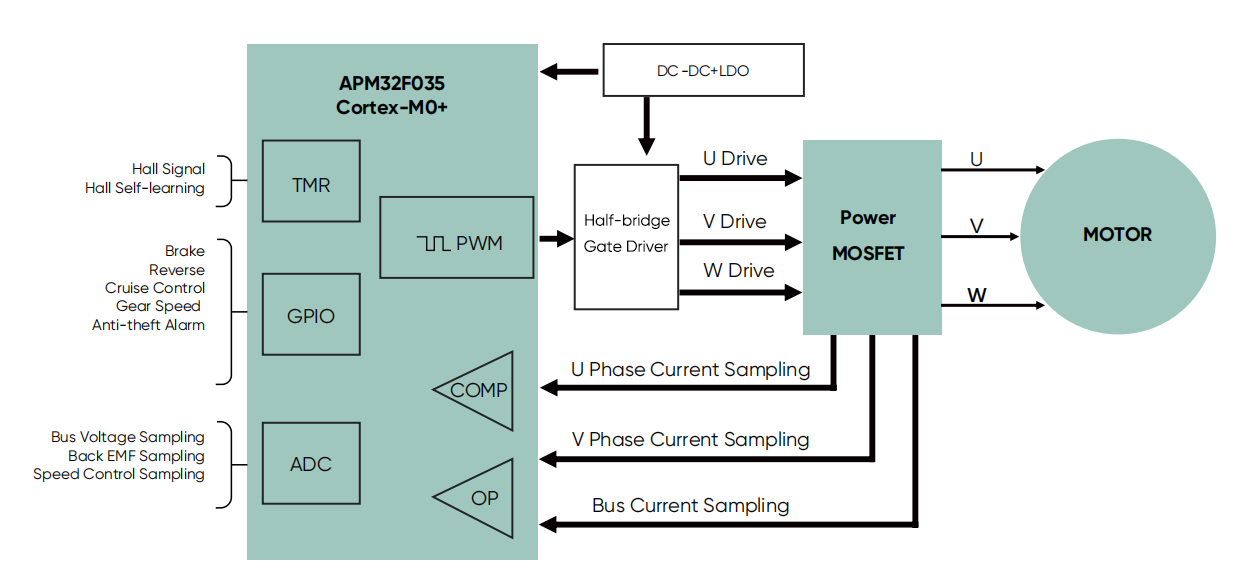
APM32F035 Electric Two-Wheeler Motor Controller Block Diagram
The APM32F035 issues control commands through methods like gear speed regulation. It synchronizes ADC sampling of bus voltage and motor phase current signals, processes them in the MCU, and combines Hall signals from TMR2 with internal algorithms to calculate the operating angle. The internal motor algorithm logic control is executed, and three pairs of complementary PWM signals are output through Timer1 to the drive chip and power devices. This drives the motor to operate efficiently, smoothly, and with low noise.
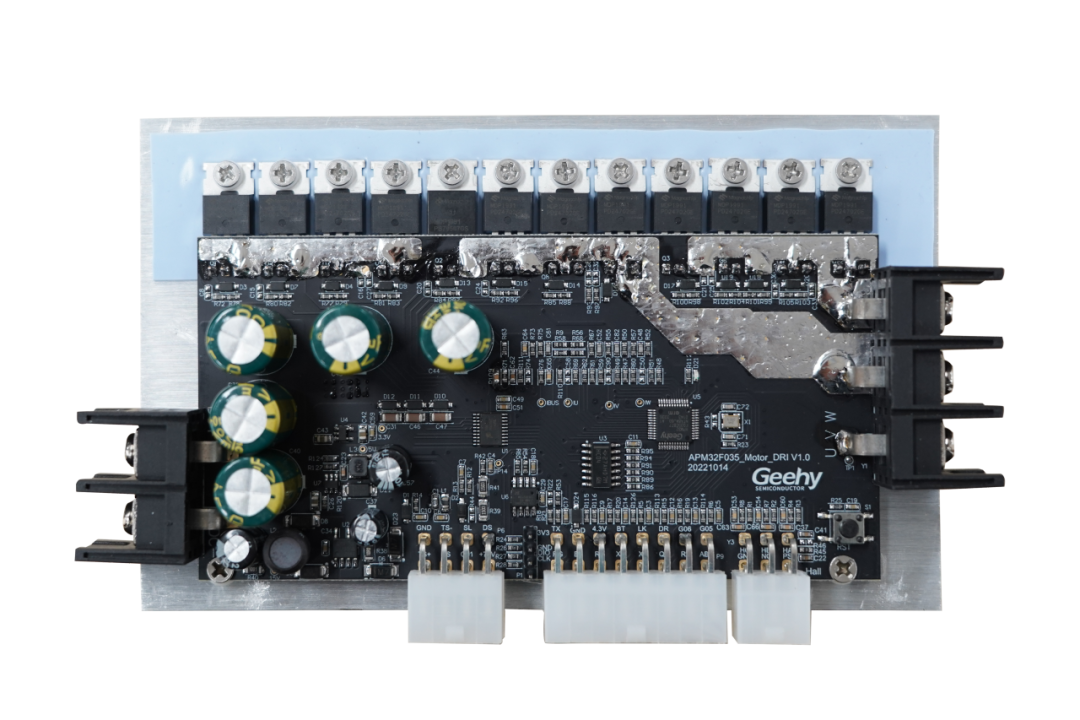
APM32F035 Electric Two-Wheeler Motor Controller Development Board
Key Features of APM32F035 Electric Two-Wheeler Motor Controller Solution
▪ FOC for improved energy efficiency and extended range.
▪ Integrated op-amps and comparators for cost-effective design.
▪ Hall learning andabsolute zero detection, with multiple installation modes.
▪ Hall compensation to enhance motor running efficiency.
▪ Torque control for quick response to load changes, capable of starting under rated load on a slope.
▪ Electronic braking and E-ABS for enhanced safety.
▪ Supports UART and CAN communication for high-end applications.
Key Advantages of APM32F035 Motor-Dedicated MCU
▪ Arm® Cortex®-M0+ core with a high frequency of 72MHz.
▪ Flash 64KB, SRAM 10KB, BootLoader 4KB.
▪ M0CP coprocessor for efficient complex calculations.
▪ Analog peripherals: OP-AMP×4, COMP×2, 12-bit ADC×1.
▪ Digital peripherals: SPI×1, U(S)ART×2, I2C×1, CAN×1, DMA.
▪ Motor-dedicated PWM: Supports complementary, braking, and M0CP linkage.