The Battery Management System (BMS) plays a critical role in electric vehicles, and manufacturers are continuously optimizing it to enhance performance. Within the BMS, the Battery Management Unit (BMU) is responsible for key functions such as current detection, insulation monitoring, State of Charge (SOC) estimation, capacity tracking, alarm management, charge/discharge regulation, and remote monitoring. The BMU includes a microcontroller system, a charge/discharge management unit, a CAN communication network for collecting data from battery cells, and control units for total voltage/current detection and insulation monitoring.
In the BMU master control module, accurate data collection, intelligent state estimation, and efficient management ensure smooth battery operations. This requires a robust automotive-grade MCU that adheres to functional safety and reliability standards, guaranteeing vehicle safety and enabling the BMU to gracefully degrade or shut down in the event of anomalies. Geehy’s BMU solution, powered by the G32A1445 automotive general-purpose MCU, supports voltage, current, and insulation detection, as well as charge and discharge management for the battery pack. It monitors battery conditions in real time, processes data from subsystems, and develops strategies to ensure optimal safety. The onboard CAN transceiver, load driver, and pressure sensors enable inter-board communication, high-side driving, and pressure detection.
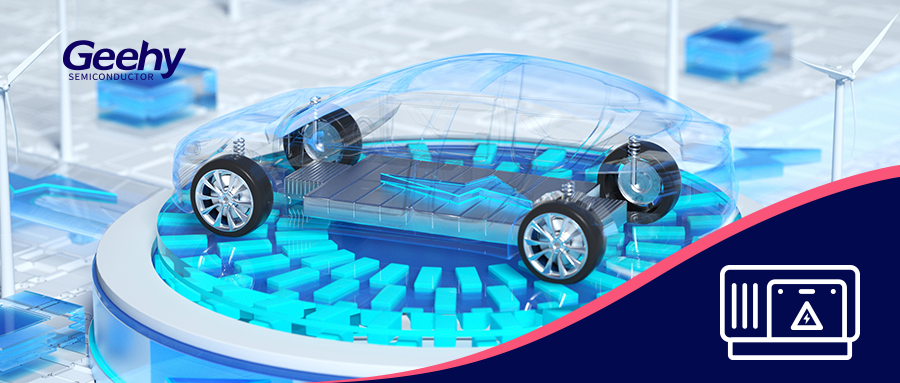
Overview of the G32A1445 BMU Solution
The G32A1445 MCU, certified with ISO 26262 ASIL-B and AEC-Q100 Grade 1 standards, serves as the primary controller. It connects to the acquisition module via a high-speed CAN interface, processing real-time battery data to develop dynamic management strategies. The MCU controls various battery operations, including thermal management, balancing, charging, discharging, and boundary management, while also exchanging information with both the vehicle and charging station. Its versatile external interfaces include voltage and temperature acquisition inputs, fan and heating control outputs, CAN2.0/CAN-FD interfaces, RS485, switch inputs, and high-voltage relay control, making it ideal for a wide range of applications.
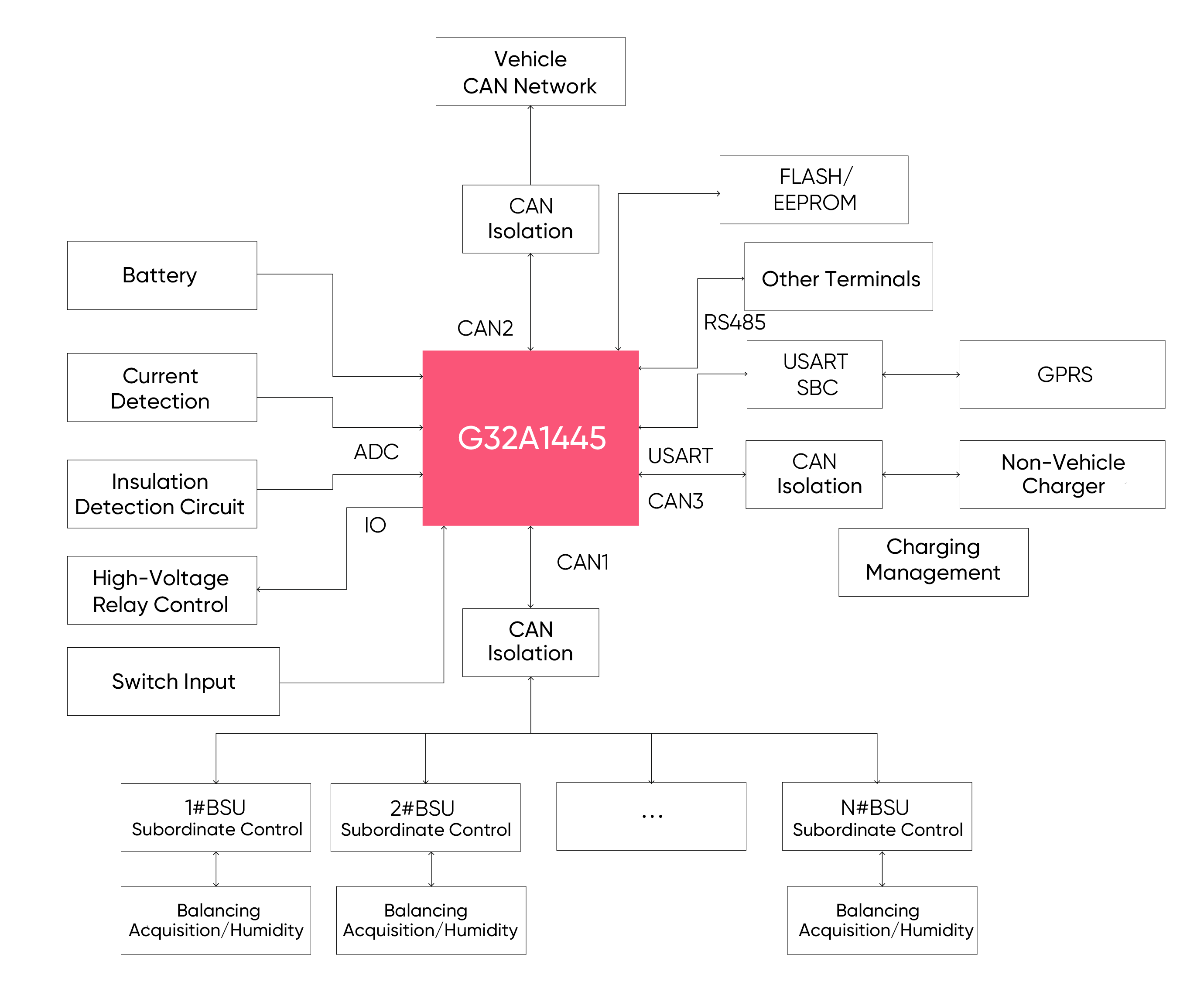
Block Diagram of the G32A1445 BMU Solution
Features of the G32A1445 BMU Solution
- Provides multi-channel control output interfaces with isolated high-voltage relays.
- Supports pressure sensor monitoring to detect thermal runaway events.
- Includes three isolated CAN networks to connect with subordinate CAN, vehicle CAN, and charging CAN.
- Offers rich peripheral configurations for efficient external design interaction.
- Enables voltage detection, overvoltage/undervoltage diagnostics, and charge/discharge control.
- Facilitates battery heating and cooling functions.
- Complies with DC charging station communication protocols.
Key Features of the Automotive General-Purpose G32A1445 MCU
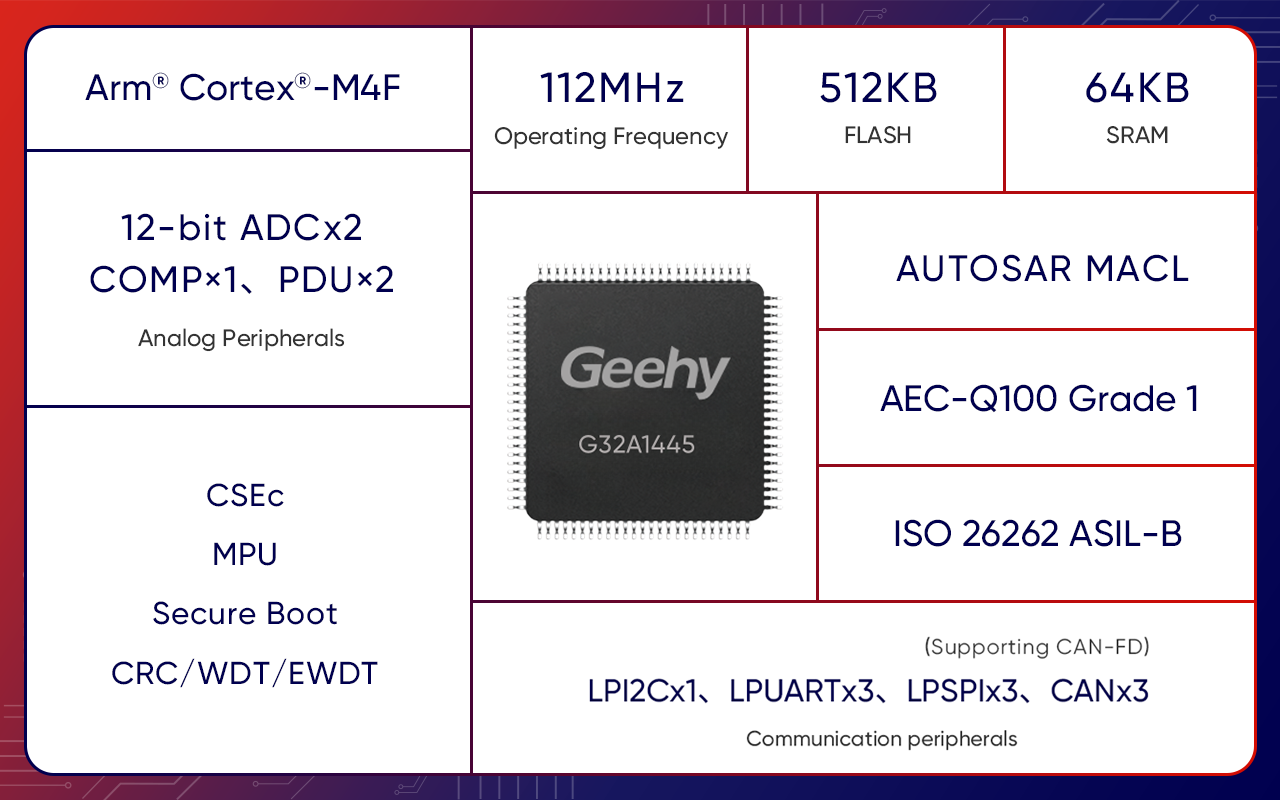
The Geehy G32A1445 MCU is equipped with advanced peripherals to support BMU communication upgrades. Its three CAN channels, all supporting CAN-FD, offer a maximum data length of 64 bytes and a bit rate of up to 8 Mb/s. The CAN-FD protocol enhances the existing CAN bus without altering its core functionality, allowing for simple program configuration changes during upgrades to CAN-FD. Additionally, the G32A1445 features built-in high-capacity FLASH memory for recording operational data, reducing the need for external memory and lowering overall costs.